The printed electronics industry, although it has existed for decades, is now experiencing a new phase of accelerated growth thanks to recent material advances and major innovations. These developments offer compact, lightweight, flexible, and low-cost solutions, ubiquitous in modern devices. Their role, often invisible, continues to play a crucial part in enhancing the functionalities of medical devices and improving the quality of care.
The most notable innovation in recent years is the emergence of printed sensors, which allow real-time monitoring of various physical and chemical parameters. Their integration into medical devices enables continuous detection, paving the way for numerous applications in health, fitness, and medical diagnostics.
Towards a Connected Medicine
Imagine a near future where a patient suffering from cardiovascular disease receives a real-time alert about an impending stroke, thanks to a printed biosensor integrated into their glasses. This technology instantly sends information to their medical team and loved ones, allowing rapid intervention to prevent brain damage. This scenario, once science fiction, is now possible thanks to printed sensors.
These technologies enable continuous monitoring and precise interventions, thus improving patient care and reducing the risks associated with medical emergencies.
Printed Sensors: Biosensors vs. Biometric Sensors
In the medical world, printed sensors come in two major types: biometric sensors and biosensors. Biometric sensors are primarily used to identify unique physical characteristics such as fingerprints, facial recognition, or voice, often for security purposes. In contrast, biosensors measure biological parameters for medical diagnosis and patient monitoring, such as blood glucose, cardiac activity (ECG), or brain activity (EEG).
These biosensors allow continuous and non-invasive monitoring of patient health, with the possibility of integrating these sensors into wearable devices such as smartwatches, medical patches, or even implants for more precise and constant monitoring.
A Revolution in Production
At DOREY Converting Systems, we understand the importance of fast, flexible, and precise production to support this medical revolution. Our all-in-one machine, which integrates lamination, rotary die-cutting, laser, and ablation in a single operation, offers an ideal solution for the manufacturing of these next-generation printed electronic devices. It meets the growing needs of connected medical devices while reducing costs and increasing productivity.
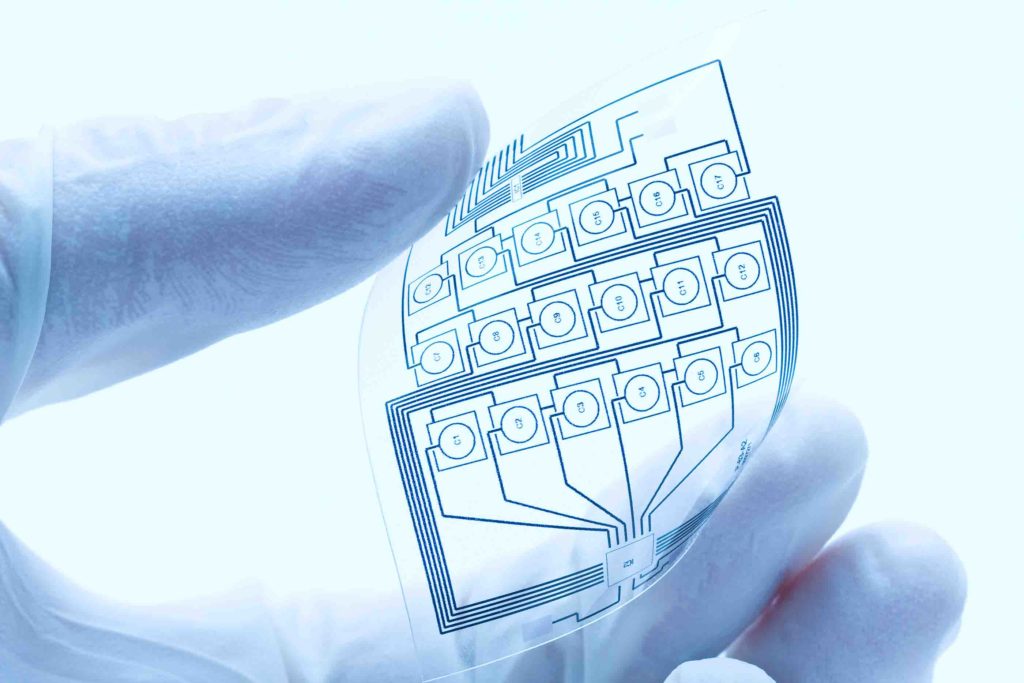
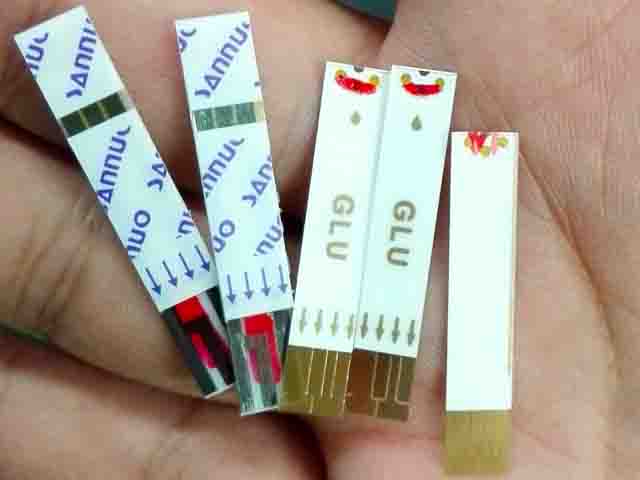

Advances in Manufacturing: Screen Printing and Functional Inks
Recent innovations in screen printing and the development of specialized functional inks now make it possible to produce sensors with increased precision. These inks are biocompatible and even transparent, allowing for the creation of discreet, comfortable wearable devices with no noticeable visual impact. This flexibility is crucial for medical applications where the comfort and acceptance of the device by the patient are paramount.
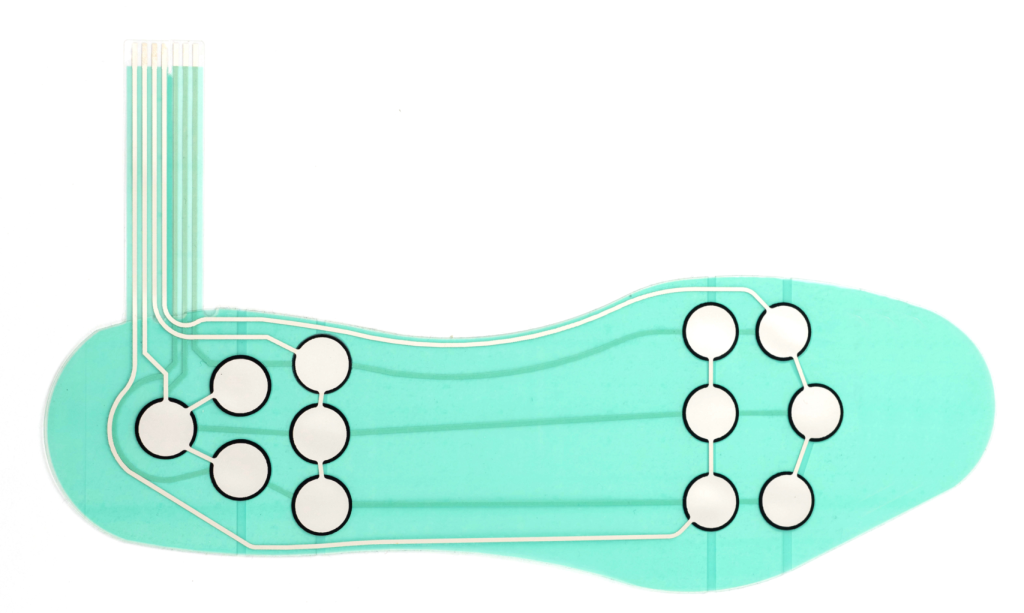
Towards Improved and Personalized Medical Care
The integration of printed sensors into medical devices is not only transforming the way care is delivered but also opening new avenues for more predictive and preventive medicine. These sensors offer continuous monitoring solutions, thus improving diagnostic accuracy and enabling quick reactions in case of emergencies.
Printed electronics and printed sensors are redefining how medical devices are designed and used. Thanks to their flexibility and reduced cost, these technologies allow for increased personalization of healthcare, while making medical devices more accessible and effective.
Our rotary die-cutting and single or multi-layer lamination machines allow for continuous and reliable mass production of your printed electronic components, whether simple or complex. We offer solutions adapted to the needs of this rapidly changing industry, with the most extreme precision on the market for your most demanding products.